Heat Recovery Solutions

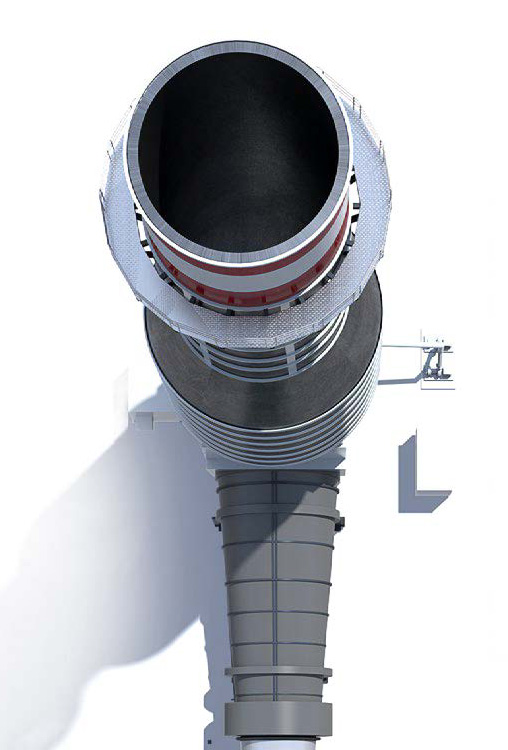
Accelerating the path to sustainable energy
With our customized Exhaust & Diverter Solutions portfolio, NEM Energy complements and supports the transition towards a decarbonized and sustainable energy environment.
We are experts at managing demanding gas turbine exhaust parameters, such as ever increasing flue gas mass flows, high turbulences and ever rising exhaust temperatures, combined with severe noise attenuation requirements.
NEM Energy’s centre of competence for exhaust systems is specialized in simple and combined cycle exhaust stacks & diverter systems, covering the full range of gas turbine applications; from industrial aero-derivative to large frame heavy duty machines.
The expert knowledge we have gained in more than seventy years of experience, is focused on designing and supplying gas turbine exhaust systems, ducting, diverters and stacks, including silencers, guillotine dampers, HRSG stack dampers and louver dampers.
Exhaust Gas Bypass Systems

Exhaust gas bypass systems contribute operational flexibility, efficiency and safety to a combined cycle power island. The heart of any bypass system is the diverter damper. NEM Energy diverter dampers combine state-of-the-art design principles and technology with more than seventy years of experience and empirical field data.
The result is that NEM Energy diverters have earned a reputation as the safest and most reliable dampers in the industry. While based on a high degree of standardization, diverters can also be custom-engineered to meet the specific combustion turbine’s characteristics, as well as the project’s individual requirements.
The stacks in particular are always designed to project specifications, such as height, design codes, acoustic requirements, environmental loads and applicable aviation warning regulations.
Simple Cycle Exhaust Gas Stacks
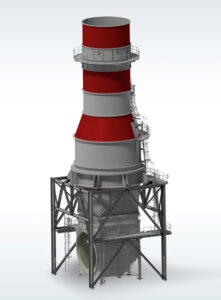
Simple cycle power plants consist of a combustion turbine and an integrated chimney or exhaust stack.
Many power island projects start with a simple cycle design in order to minimize initial capital costs, reduce equipment installation time and enable power generation as quickly as possible. Traditional simple cycle exhaust systems are typically designed with a self-supported exhaust chimney or stack. This design is used when no future conversion to combined cycle operation is envisaged, but it is not cost and time effective for future extension to combined cycle configurations. In such a case, stacks with an external support steel structure and elbow ducting present an easy to convert solution.
The NEM Energy design portfolio covers both versions: the base mounted as well as the elbow duct design.
Guillotine Dampers and Blanking Plates
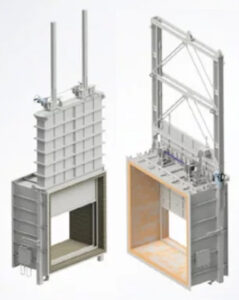
Guillotine-type blanking plates are extensively used in exhaust gas bypass systems as a secondary shut-off device in conjunction with the diverter damper in order to create a “man safe” environment within the downstream HRSG when the combustion turbine is operating.
As stand-alone solution, the guillotine damper type will typically utilize a temperature-proof design with rack and pinion drive system and a gas-tight, fully enclosed bonnet.
Almost the full cross-section of the duct is available once the guillotine blade is fully retracted, resulting in a very low pressure drop. Depending on the application, designs with or without seal air are possible.
Stack Dampers
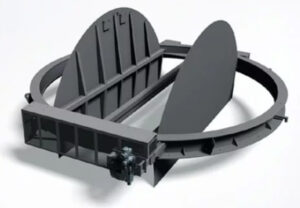
The primary function of an HRSG stack damper is to slow down the cooling rate of the HRSG between gas turbine starts.
By minimizing the dwell time necessary for HRSG restart, thermal stresses for pressure parts of the HRSG are reduced, resulting in an increased life time.
Stack dampers also prevent rain from entering the HRSG during sustained shutdowns. The most advanced stack damper design incorporates aerodynamic aspects and an improved drive system, which provides independent overpressure relief on the blades in case of process upsets.
NEM Energy stack dampers for HRSGs come in standardized, parametric 2-blade- or individual 4-blade designs. The dampers can also be retrofitted to existing HRSG stacks relatively quick and easy, utilizing either the complete damper configuration with frame or the Stack Damper Retrofit Kit.
Louver Dampers
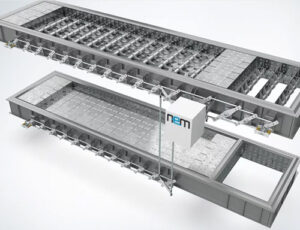
Louver dampers by NEM Energy are robust flow control and/or shut-off devices used in flue gas ducts, specifically designed for the demanding environment inherent in combustion turbine exhaust installations.
NEM Energy designs and builds louver dampers in accordance with the plant-specific parameters and clients’ individual specifications, and the dampers are available in various designs, dimensions and shapes, with or without duct section (T-Box). Actuation can be manual, electrical, pneumatic or hydraulic type.
The construction materials used depend on the operating temperature and pressure, abrasive or corrosive environment and other process operating conditions. Louver dampers can be built as single or double louver versions, and are designed with either internal or external insulation.
Depending on the operating conditions and the required degree of tightness, different seal arrangements are available. Double louver dampers or twin-blade lover dampers with seal air injected in-between both blade planes provide a hundred percent tight barrier against gas leakage.
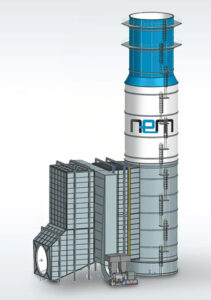
Tempered Selective Catalyst Reduction systems, simply referred to as T-SCRs, by NEM Energy offer an effective and efficient way of reducing Nitrogen Oxides emissions from open cycle gas turbine plants, while maintaining efficient operations over a wide range of load cases as well as increasing catalyst lifetime.
NEM Energy has developed a solution for NOx reduction in Open Cycle Gas Turbine (OCGT) plants using tempering air in an SCR system. By mixing the flue gas with the incoming air to a moderate temperature before it enters the catalyst, tempered air SCR systems (T-SCR) achieve effective NOx reduction without the disadvantages afore mentioned of the hot SCR.
NEM Energy has developed a unique method to uniformly mix the flue gas with the tempering air and ammonia, in a self-correcting system enabling compliant use of the SCR over the entire operating load range of the gas turbine. By saving on the capital and operational expenses, the T-SCR system offers the lowest total cost of ownership. The use of tempered air facilitates more efficient NOx reduction while enabling operational flexibility, making it a preferred option for achieving emission reduction targets in OCGTs